倉庫内作業を見える化する活動量計の実力
装着するだけで、手間をかけずに作業員の動作を自動で収集できる。そんな夢のようなデバイスがリストバンド型の活動量計だ。SBS東芝ロジスティクスでは、このデバイスを活用して得た作業員の作業実績データと標準工数のギャップを検証することで、自社のみならず、顧客の倉庫内作業の改善提案にも取り組んでいる。すでに、作業員の歩行ペースの最適化や商品の配置変更などに役立てられており、着実に効果を生み出している。
プラットフォーム事業部 4PL開発室 室長の石川 祐太と、物流改革推進部 業務標準化担当 主任の安部 博之に、開発の経緯や導入効果、活動量計の今後の展望などについて聞いた。
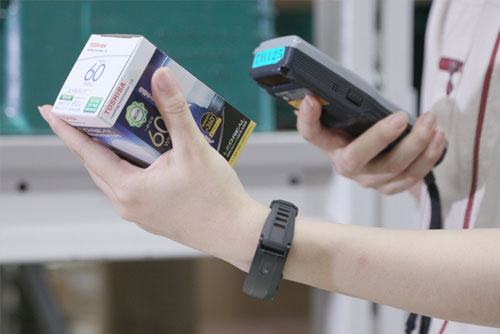
物流業務の可視化に対する期待値は高かった
深刻化が進む人手不足を背景に、物流現場の生産性の向上は業界共通の急務の課題だ。そのため多くの企業が、作業工数の削減や人員の適正配置に取り組むなど倉庫内作業の改善に努めてきた。しかし現実的には、倉庫内で働く作業員の動きを把握するのは容易なことではない。物流作業は、製造工場のような定位置・定作業とは異なり、作業員の対象製品が日々変わるという非定常で変則的な作業だからだ。
さらに、現場観測の方法として広く用いられている、IE(Industrial Engineering)手法をベースとしたビデオ観測や定点観測にも、いくつか欠点がある。データ取得が特定の作業者、特定の日時となるため 必ずしも職場全体の状況を表しているとはいえないのだ。さらに手間がかかる割にはデータ量が少ないため、多面的な分析ができないという欠点もあった。
「物流業務を可視化することの難しさは、当社だけでなく物流業界全体の古くからの悩みでした」と話すのは、プラットフォーム事業部 4PL開発室 室長の石川 祐太。倉庫内の実態をとらえるための信憑性の高いツールが不足していたという。
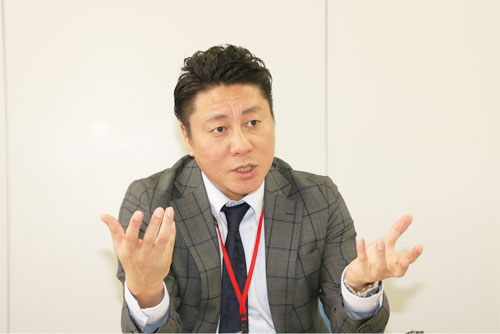
そこで当社では、東芝デジタルソリューションズ(株)が開発した動作推定技術に着目した。これは、リストバンド型ウェアラブルデバイスに装備されているセンシングを用いている。物流改革推進部 業務標準化担当 主任の安部 博之は、「以前より、「この作業であれば、これくらいの時間がかかる」といった、目標値となる標準工数の設定に取り組んできました。活動量計を使って人の動作を区分できる技術があることを知り、これらを組み合わせることによって、倉庫内作業の改善提案につなげることができるのではないかと考えました」と、当時を振り返る。
推定できる作業は、「台車移動」「手作業」「歩行」「静止」の4区分。活動量計に組み込まれているX軸、Y軸、Z軸の3軸の加速度センサによって、作業員の動作を推定できる仕組みになっている。作業員は、腕時計を装着するような感覚でいつも通りに作業をすればよい。活動量計のデータからは、誰がどこで、どんな商品に、どれくらいの時間がかかったのか、ということを把握できるようになり、さらに倉庫管理システム(WMS)のデータと結合させることで、実績と目標のギャップの見える化を実現させた。
「データで明らかになるのは、あくまでも現場の実態です。そこから課題を解決するところまで結びつけるのが難しいところ。「こういうパターンのときは、このような解決策が考えられますよね」といった改善案の定型化には非常に苦労しました」(安部)
活動量計の構想から製品化までに費やした期間は、2年以上にも及んだ。自社倉庫内で作業者に実際に装着してもらい、繰り返しテストも行ってきたという。
「現場からの評価もとてもよかったです。今までなんとなく無駄だと思っていたことが数値として表れるのがいいねと。そういう言葉は開発者としてとても励みになりました」(安部)
信頼ある実態データから改善活動につなげる
活動量計のリリース以降、顧客からの反応も好調だ。装着するだけで簡易にデータが取れるという点が、業界全体の従来の悩みを払拭する結果となったのだろう。さらに、これまでは「なんとなく」でとらえていた現場の課題に対し、エビデンスに基づきながら改善を進められることも、業界に与える衝撃は大きかった。「大手文具メーカーや家電メーカーなども大きな興味を示してくれている」と話す石川の言葉からも、業務を可視化する重要性が広く理解されていることがうかがえる。
ただし、取得した結果の精度に対する不安の声も少なくなかったのも事実。そのことに対して石川は、「4区分の動作が本当にその動作を表しているのか、ということに安部ら開発者は非常に苦労していました。しかし今は、成功率は向上しています。かなり精度の高いデータを取ることができるようになりました」と、胸を張って言い切る。
顧客の現場においてもすでに改善活動が進められており、いくつか成果も表れている。例えば、雑貨の卸業務を行っている企業の倉庫では、「歩行」と「台車移動」の区分で、目標とする標準的な速度との差異が意外と大きく表れていた。また、「手作業」も標準工数よりも大幅に時間がかかっているという事実も明らかになった。 「「歩行」「台車移動」に対してはLED等の利用で速度の目安を作業者に認識してもらう、「手作業」については商品を収納する際の整理に時間がかかっていたことから商品の大小を考慮した商品配置にすることで整理の時間を短くできないかといった提案を行っています 」(安部)
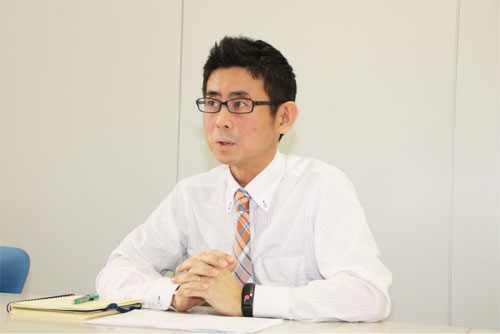
また一方で、生産性向上の解決策の一つとして、最近盛んに話題になっているのが倉庫内への自動化設備の導入がある。「設備投資をして自動化を検討したいが、現場の実態がわからないため効果試算ができない」というニーズにも、応えることができるのが活動量計の強みだ。実際にある製造メーカーでは、自動化によって作業員の移動を少なくできるのではないかと想定し、現時点での移動がどの程度なのかを把握するために活動量計での測定を行った例もある。
「移動時間は、作業時間の10%未満だったという結果がデータとして示されました。こうしたケースでは、設備の自動化の効果はあまり大きくないことが予想されます。その一方で、4区分の動作の分析データに見られた結果から、棚の使い方によって生産性の向上を図れることも加えて報告させていただきました」(安部)
「インパクトが大きいのは、人員がたくさんいるところや、取り扱いアイテムが多いところ、商品の形状にバラつきがあるところ。こうした現場の作業に関しては、効果が非常に大きいと感じています」(石川)
人の動きがあるシーンなら活動量計の可能性は無限大
これからの課題について安部は、「フォークリフト作業の可視化に力を入れたい」と話す。なぜなら倉庫内には、フォークリフトに乗っている作業員もおり、中には半数がそれにあたる倉庫もあるからだという。特に倉庫の1階は、トラックが着いて荷物を下ろし、また荷物を積んで出庫するといった具合に頻繁に出入りが続く場所。人はもちろんだが、フォークリフトも縦横無尽に動き回っているため、どうしても動作を制御しきれないエリアなのだ。地上にいる作業員のみが対象となっている活動量計を進化させ、フォークリフト作業への展開が必須だと考えている。
「将来的には、ディープラーニングを活用して今の活動量計と同じようにフォークリフト作業の動作も推定できるようになると思います。現時点では、別のセンサを組み合わせて、分析対象として取り込んでます 」(安部)
また今後、そうした煩雑な1階エリアの業務改善に取り組もうとしたとき、「どこで」という位置情報が重要なキーワードになると石川は断言する。現在でもWMSとのデータと付け合わせると位置情報がわかるが、活動量計単体で位置情報が取得できれば導入がスムーズになり簡単に必要な情報が取得できる。そうすればより詳細な現場の情報が把握でき、多くの現場での生産性の向上に踏み込んでいけるはずだ。
「高度な技術は、物理的な距離をぐっと近づけたり、時間を短縮したりします。活動量計もその一つのツールになるとよいですね。今は、目に見えている範囲で行っていることですが、例えば、遠く離れた現場の様子がリアルタイムで見えるようになるとか、活用の幅も広げていきたいです」(石川)
さらにもっといえば、これは物流業界に限ったことではなく、人が動いているところであれば可能性は無限に広がっていくだろう。
最後に石川は、「これからの日本は、生産人口の減少という大きな問題に直面します。恐らく、外国人の労働者がどんどん日本にやってくることでしょう。すると、言語が通じない相手に対して、仕事をお願いする機会が確実に増えていく。そうしたときに、活動量計を用いたソリューションは、単純で標準化された作業や達成目標のようなものの設計図みたいな使い方ができるんじゃないかなと思っています」と、今後の活動量計の飛躍に胸を膨らませながら語った。
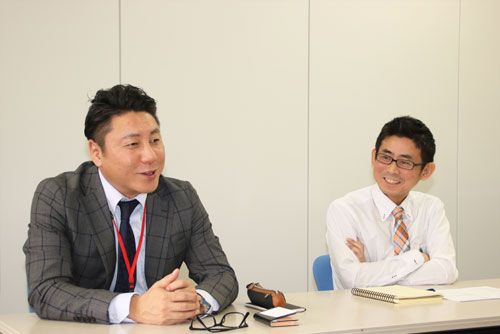
関連ページ
- コンサル事例:倉庫状況の可視化
- コンサル事例:海外保税区活用
- コンサル事例:医薬品メーカーの物流設計
- コンサル事例:保管現場改善支援
- コンサル事例:物流拠点集約
- コンサル事例:拠点集約による物流コスト削減
- 家電物流事例:新物流体制の構築
- 家電物流事例:共同プラットフォーム活用
- DFL事例:コンテナ積載効率の改善
- DFL事例:製品&包装見直しによる積載効率改善
- DFL事例:ロジコストの最小化
- 移転事例:国立大学の研究室
- モーダルシフト事例:半導体輸送
- IT/TEC事例:グローバル在庫管理
- IT/TEC事例:棚搬送ロボットシステムの導入
- IT/TEC事例:画像一括検品システム
- IT/TEC事例:帳票アプリ導入による作業時間・コスト削減
- IT/TEC事例:バース予約システム導入
- IT/TEC事例:AI活用の検知警報システム
- IT/TEC事例:AGV導入の取り組み
- 活動量計事例:庫内作業の工数削減
- 活動量計事例:倉庫内作業の見える化
- 使用済み段ボールの再利用
- 女性が活躍する物流現場
- 3PLとは?メリットとデメリット